The Super Finishing process is suitable for many categories of engine and gearing components. The process can be applied to:
High performance automotive
Motor sports
Motocross
Vintage & Classic motorcycle engine and gear components
Large capacity engine components
Marine, Aviation & Industrial component
In industries, such as high performance automotive, motorcycle racing, and motorsport in general, every component must work to its fullest potential. Competitive racing teams are always looking for maximum performance gains often through incremental improvements.
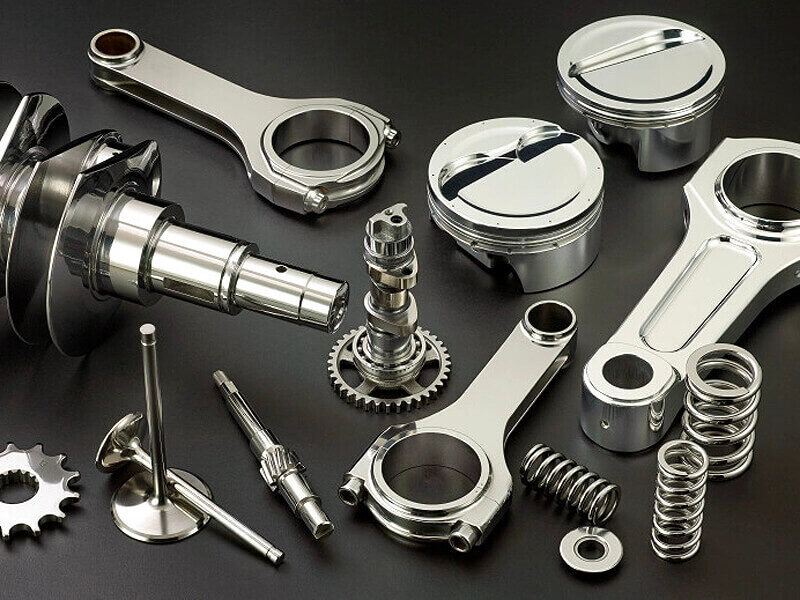
These performance-based applications and sports stress metal components to the very limit of their endurance. Wear and friction is the enemy, taking vital fractions of a second off lap times and sometimes leading to total part failure.
With our super-finishing process, the energy normally lost to friction is now available in the form of increased power output. Once friction is reduced, the engine will run cooler allowing for longer durability of parts and fewer failures.
GMD Restorations state-of-the-art equipment can provide a super-finish on a range of different gearboxes, engines and other load-bearing components.
What is Isotropic Super Finishing?
When metal components are manufactured, machined, or altered, a surface texture is generated.
These processes, such as cutting, grinding, lapping, abrasive blasting, honing, milling, etching, chemical milling, etc., result in a texture that has peaks and troughs. This surface texture will vary between a vertical, horizontal, radial, circular and cross-hatched pattern.
When these rough surfaces are in contact with each other within a mechanical system such as an engine or transmission, friction, stress and heat can lead to a failure of the component within that system.
The Super Finishing process uses a chemical and vibratory process to lower the surface texture roughness to as close to zero as possible, this results in an Isotropic Surface Finish.
This isotropic surface finish then allows the metallic surfaces to operate with reduced friction, enhanced efficiency, lower heat generation, increased lubricant efficiency and lowered metallic stress.